Principles and characteristics of laser marking machines.
Laser Engraving Machine Price List
The prices of laser markers vary greatly depending on the power, and when choosing one, you need to consider the type of material to be processed, the processing efficiency, and the application environment.The article provides a breakdown of the price ranges for popular models, such as those with 20W, 30W and 50W lasers, and explains the strengths and weaknesses of fiber and CO2 laser machines. It also provides tips for avoiding common pitfalls in the purchase process, so that companies can buy high-quality laser engraving equipment at a reasonable price.
Laser cleaning machines
Laser marking and cleaning machines use high-precision lasers to mark and clean. The former uses a non-contact method to engrave a permanent pattern, while the latter can remove surface impurities without causing any damage.Laser cleaning is environmentally friendly, efficient, and has low maintenance costs, but it has the limitations of high initial investment and limited surface area. It is suitable for the restoration of precision parts and industrial cleaning. When in operation, safety precautions and parameter adjustments must be carefully considered.
Parts for laser engraving machines
When selecting components for a laser marking system, three factors need to be taken into account: compatibility, quality certification, and cost control.The key components are the laser generator, galvanometer system, and field lens. When buying, one should combine equipment parameters and actual processing needs.The suggestion was made to establish a record of the life of parts, and through recording actual data on the use of the laser tube, focusing lens and other easily damaged parts, to establish a scientific plan for stockpiling spare parts.When choosing a supplier, they must verify quality control reports and factory certification. In order to optimize maintenance costs, they must guarantee the stability of the equipment.
Carbon Dioxide Laser Marking Machine
The CO2 laser marker, with its high precision and non-contact characteristics, has made a big splash in the non-metallic materials processing field.Whether the material is acrylic, wood, leather or plastic, a clear and lasting mark can be made by adjusting the power and speed.The book combines practical applications with explanations of equipment operation, material selection, and common troubleshooting methods, to help users quickly master the core points of laser engraving of non-metallic materials.
Laser Engraver Repair
If your laser marking machine suddenly breaks down or produces inferior results, this self-inspection guide will help you quickly get the machine back up and running.These manuals contain practical maintenance suggestions and operating instructions, which solve common problems with laser equipment and extend the life of the machines.
Consumables for Laser Marking Machines
Common consumables for laser markers include the laser head, focusing lens, and filter cotton, among other core components. The replacement cycle of different consumables directly determines the efficiency of the equipment.It covers the selection of consumables and the maintenance of CO2 laser tubes and galvanometer systems, and helps users cut maintenance costs and prolong the life of their equipment.
Is a small laser cleaner suitable for a family workshop?
Small-scale laser cleaning devices can indeed provide a convenient solution for small-scale workshops. But when purchasing one, it is important to focus on the power, the cost of operation, and safety measures.A reasonable choice is a 80-100W model with a frequency adjustment function, which will satisfy your daily metal cleaning needs while controlling your electricity bill.It is particularly important to pay attention to the replacement cycle of consumables such as lenses, and to use professional protective equipment to ensure a safe and efficient production environment.
Laser Marking in Electronics
Laser marking and cleaning machines are becoming core tools in the electronics manufacturing industry. From marking printed circuit boards with micron-level precision to finely etching metal casings, to cleaning precision components without damaging them, these machines improve production efficiency and solve environmental problems associated with traditional manufacturing processes.UV technology is especially suitable for the miniaturization trend in electronics, and its non-contact nature guarantees a high yield of quality components. It is reshaping the production processes of 3C products.
Five Advantages of Laser Cleaning over Sandblasting
Laser cleaning technology is replacing traditional sandblasting techniques thanks to its core advantages of precision, controllability, environmental friendliness, and efficiency.From improved work efficiency to zero material damage, from long-term cost advantages to special applications, this contactless cleaning method not only reduces material consumption by 90 %, it also achieves a level of cleanliness that conventional methods cannot approach. It is particularly suited to the modern manufacturing industry, with its high standards of environmental protection and craftsmanship.
Three Techniques for Extending the Lifespan of Your Laser Equipment
Mastering the proper daily cleaning techniques for laser equipment, learning to adjust work parameters according to the characteristics of the materials, and establishing a scientific replacement schedule for parts are three maintenance methods that can effectively extend the life of the equipment.Regular cleaning to avoid damage to optical components, reasonable control of workload to prevent overheating, and the use of original factory parts to ensure system stability all contribute to keeping laser equipment in top working condition. This not only lowers the risk of accidental breakdowns, but also saves on repair costs.
Removing Rust with a Laser
The laser cleaning machine uses a high-energy laser beam to precisely remove rust from the metal surface. When operating the machine, you need to adjust the parameters based on the state of the rust layer, and pay attention to safety precautions.Compared with traditional methods, this process doesn ’ t damage the substrate, is environmentally friendly, and is highly efficient. It is especially suitable for the rust removal needs of precision parts and complex structures, and is a preferred modern method of metal surface treatment.
A Guide to Purchasing an Industrial Laser Cleaning Machine
When choosing industrial laser equipment, one should consider power adaptability, repeatability, wavelength matching, spot size adjustment, and after-sales service. Different materials and applications require different parameters. One must also pay attention to details such as human-machine interaction. Only then can one find a production tool that saves money and is efficient.
What is the difference between laser marking and laser cleaning machines?
Although laser marking and cleaning machines are both laser devices, their functions are completely different.The former is for delicate engravings, while the latter is for cleaning the surface of the object.When selecting an appropriate laser, one must consider the power requirements, the characteristics of the material to be treated, and the environment in which it will be used. A low-power laser can be used for precision processing, while a high-power laser can quickly handle industrial-scale cleaning tasks.
How can software be optimized to improve the efficiency of laser engraving?
Software optimization is the key to boosting the efficiency of laser engraving.By adjusting the parameters of power, speed, and frequency, and combining them with software functions such as layered carving and template libraries, processing time is greatly reduced.Regular maintenance includes attention to calibration of the light path and analysis of the data logs, to ensure that the equipment is always in the best possible condition.By mastering these techniques, a company can achieve a quantum leap in efficiency without having to invest in new hardware.
Cost comparison between laser marking machines and traditional mechanical engraving
The main differences in costs between laser marking machines and traditional mechanical engravers are in the areas of equipment purchases, processing efficiency, and maintenance.The initial investment is higher, but the long-term costs of materials and electricity are lower, and this is especially appropriate for small batches of precision processing.Traditional equipment is more stable for large-scale continuous production, but requires frequent maintenance of mechanical parts.When choosing a machine, you have to consider the type of order, the characteristics of the material, and the long-term operating costs.
What kind of laser engraving machine is best for a small workshop?
In order to meet the practical demands of small studios in choosing a laser engraver, the article provides a comprehensive analysis of power selection, material compatibility, core component quality and ease of operation.It highlights the different applications for different power output devices, stresses the importance of identifying misleading specifications, and reminds readers to pay attention to the costs of long-term maintenance.He recommends that customers consider 20-40 watt machines that have smart focus functions and work with popular design software, so that studios can choose a high-value laser cutter that fits their budget.
Possible Causes of Poor Marking Quality
The clarity of the mark depends on the settings, the state of the equipment, and the characteristics of the material.During maintenance, the power, speed, and frequency settings should be adjusted to find the best combination. The lenses should be cleaned regularly, and the light path should be checked to make sure that it is properly aligned.Different metals require different approaches. For highly reflective metals, it is best to pre-process the surface. Thin sheets of metal need to have their temperature carefully controlled to prevent deformation.Mastery of these practical skills can significantly improve the clarity of the markings.
What maintenance should one be aware of when using lasers for a long time?
The key to long-term stable operation of laser equipment is regular maintenance, including daily cleaning to prevent dust buildup, maintenance of the core components, and optimization of usage habits.The machine should be cleaned of dust, and the lenses of dirt, on a regular basis. The state of the cooling system should be monitored. The working parameters should be rationally set, and the ambient temperature and humidity controlled. An annual professional inspection should be scheduled.These details are effective in extending the life of the equipment and maintaining the precision of the carving, avoiding the high cost of repair.
What materials are suitable for CO2 laser engraving?
The CO2 laser engraver is mainly used to process non-metallic materials, including wood, acrylic, leather, plastics, and textiles.Avoid using metal, glass, or materials containing chlorine to prevent damage to equipment or safety hazards.Before use, the parameters need to be tested, and ventilation must be provided. Regular maintenance focuses on cleaning the lenses and inspecting the cooling system.
How can you choose the correct laser marking machine power without wasting your budget?
The choice of laser power depends on the type of material to be marked, the requirements of the process, and the budget.Soft materials require 20-30 watts of power, while metals require 50 watts or more.To avoid the waste of money that comes with blindly choosing a high-power motor, it is recommended that you test samples to determine the minimum power level that will work, and then build in a 10-20 % performance margin.They focused on balancing long-term operating costs with processing efficiency, selecting a machine type that met their needs and was also cost-effective.
The Technical Requirements of Laser Equipment for Soldering Precision Electronic Components
The technical requirements for laser equipment used in soldering precision electronic components include core parameters such as power stability, precision of the light spot, and heat dissipation capacity.In practical use, the laser's wavelength must be matched to the characteristics of the material being worked on, and attention must be paid to heat dissipation and long-term maintenance costs.When selecting a machine, you should compare actual performance indicators and combine the needs of medical, microelectronics and other sectors, to ensure that the equipment meets the requirements of precision processing while also controlling overall operating costs.
A Study on the Influence of Laser Welding Process Parameters on Weld Quality
The core parameters of laser power, scanning speed, and focal length directly affect the quality of the weld.By adjusting the power range, you can avoid burning through the workpiece or failing to fuse the materials. By controlling the speed of movement, you can obtain a continuous, uniform weld. By adjusting the focal point, you can control the distribution of energy.By optimizing parameters and using protective gas, the density and mechanical properties of the weld can be significantly improved. When used in practice, the thickness of the material and the type of joint must be taken into consideration.
Suggested Budgetary Planning for Laser Welding Equipment for Small and Medium-Sized Enterprises
When a small or medium-sized enterprise is considering purchasing a laser welding machine, the first thing it should do is to clarify its processing needs. It should then select a machine with appropriate power and functionality.Budget allocation should take into account the cost of equipment, consumables, and maintenance. Be wary of the pitfalls of multifunctional machines and used equipment.He suggests that buyers should first choose a local agent with long-term warranty coverage, then seize promotional opportunities to cut costs and achieve the most optimal balance between price and performance.
Laser Welding Machines in Automobile Parts Production
Laser welding machines have demonstrated a significant advantage in automotive parts production, with high-precision, high-efficiency welding techniques that enhance the strength and lifespan of key components.In fact, this technology can be used to weld car doors, batteries, and other components, and it saves 30 % more energy than traditional welding methods.When selecting equipment, it is important to focus on the compatibility of materials, automation integration, and maintenance costs. A reasonable layout can greatly lower production costs and meet environmental protection requirements.
Solutions to Common Problems in Welding High-Reflectivity Metals
In order to overcome the problems of energy reflection, insufficient melt depth, and equipment damage that arise when welding highly reflective metals, researchers have improved the combination of power and speed parameters, used pulse-mode control to reduce splatter, and strengthened pre-welding surface treatment (cleaning / coating) to improve weld quality.At the same time, we emphasize the maintenance and protection of lenses and the selection of protective gases to help operators reduce production costs and extend the life of equipment.
Daily Maintenance of Industrial Laser Welding Equipment
Daily maintenance of industrial lasers directly affects their lifespan and the accuracy of the processing they do. The most important things to focus on are the cleanliness of the mirrors, the condition of the cooling system, and parameter calibration.Periodic cleaning of dust and oil can prevent abnormal optical paths, and water-cooling units should have their filters changed regularly to ensure efficient heat dissipation. Laser tubes and protective lenses should also be replaced in a timely fashion according to actual workload.Mastering the maintenance cycle for each part of the equipment and setting up a ledger of maintenance work can effectively lower the rate of equipment failure and prolong the life of equipment.
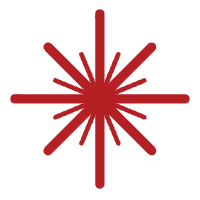
Provides laser marking machine principle characteristics, accessories and software, industry applications, technology optimization, procurement decisions, material technology, technology trends, user scenarios, upgrade solutions, special needs and other related content.