Advanced Laser Marking Technology and Optimization of Industrial Processes.
Medical laser engraving
The book provides a detailed explanation of the principles and key points of operation of medical laser marking machines, including material adaptability, parameter setting techniques, and process optimization.For special requirements of surgical instruments and implants, they share advanced solutions such as positioning and calibration, and micro-engraving, and also provide practical suggestions for equipment maintenance, helping medical equipment manufacturers achieve permanent markings that are safe and compliant.
Laser Marking Machine
When choosing a laser marking machine, the size of the marking area directly affects the model and power configuration of the equipment.From the perspectives of material adaptability, processing precision, and cost-effectiveness, he explains how to match the right laser marking machine to the size range and complexity of the actual work piece.By using the core parameter comparison chart, users can avoid the low processing efficiency and waste of equipment resources caused by choosing the wrong model.
Calibrating the Laser Marking Machine
A laser marking machine's beam path is critical to the quality of the finished product. This article provides a detailed explanation of the five steps involved in calibrating a beam path, including the use of red light to locate the focal point, and adjusting the angles of the mirrors. It also recommends the use of a cross-shaped calibration plate and a power meter, and offers tips on how to use these tools to quickly solve common problems such as misaligned focal points and uneven engraving.
Laser Marking Machine
Want to improve the results of laser marking and engraving? Reasonable adjustments to parameters are key.By combining laser power, speed, and frequency with material characteristics and graphic complexity, a practical method of adjustment is provided.By grasping the techniques of matching different metal and plastic materials with different parameters, the user can learn to achieve fine engraving by adjusting the focal length and optimizing the fill mode, and thus improve the clarity of the mark and the speed of the engraving process.
Laser cutting
The key to good cutting is precise focus, and the trick to getting it right is to observe the sparks, do trial cuts, and apply the rules of thumb.Operators must be aware of the effects of temperature changes on the equipment. By combining the "three looks and one listen" rule of thumb, even a novice can gradually develop the ability to quickly focus the beam, ensuring cutting accuracy and equipment longevity.
Automated laser marking
In response to the needs of manufacturers for intelligent upgrades, we offer a complete design solution for integrating laser marking machines with automated production lines.It provides key technologies in equipment selection, industrial communications protocol integration, and material tracking system interlinking. By adopting a modular integration strategy, it helps the electronics, auto parts, and medical equipment industries to realize efficient, precise automation in labeling and processing, reduce labor costs, and increase overall production line efficiency.
Laser Processing: Environmental Requirements and Equipment Protection
The environment in the laser processing workshop needs to be precisely controlled in terms of temperature, humidity, and ventilation. It is necessary to prevent moisture from damaging the equipment, while also ensuring adequate air circulation.Equipment protection requires a complete system, from daily maintenance and safety devices to power protection. Regular maintenance can effectively prolong the life of equipment.The operator needs to master emergency procedures for common problems, and only by following the rules and practicing scientific management can the laser processing process be both safe and efficient.
Parameters for Laser Cutting and Engraving
The key differences between laser cutting and laser engraving are in the laser's power, frequency and movement.Cutting requires higher power with low-speed continuous operation, while engraving depends on high-frequency pulses and fine spot control.Different materials require different parameter combinations. For metallic materials, the focus is on power threshold, while for non-metallic materials, it is on the balance between speed and heat dissipation.Mastery of these parameters can dramatically improve processing efficiency and the precision of the finished product.
Avoiding the Pitfalls of Consumables
When selecting laser equipment, you can't just look at the price tag. The key is whether it matches the actual processing needs.From defining the usage scenario to controlling core components, attention needs to be focused on laser performance, software compatibility, and auxiliary system configuration.The selection of consumables requires a balance between cost and quality, and a good understanding of lenses and gas usage can help to reduce operating costs.In terms of maintenance, he suggests establishing a system of regular inspections in order to prevent problems before they occur.
How to Tell When the Mirrors of a Laser Cutter Need to Be Replaced
The condition of the mirrors in a laser cutting machine has a direct impact on the quality of the cut and the machine's lifespan.By observing a drop in the quality of the cuts, or yellowing or scratches on the lenses, and combining this with the information from the strong light inspection and the equipment's alarm signals, it is possible to quickly decide whether the lenses need to be replaced.Regular maintenance and replacement of components is required to keep the system running smoothly, and it is best to replace parts with those made by the manufacturer.
Common Mistakes Made by Laser Engravers
He also explains how to avoid common mistakes, such as improper focusing, and the importance of maintaining equipment.
Laser Cutting Parameters for Different Materials
The book explains in detail the key parameters for laser cutting of both metal and non-metal materials, including laser power, cutting speed and gas pressure. It also provides practical advice on cutting common materials such as stainless steel, aluminum, acrylic and wood, as well as a quick troubleshooting guide. This will help operators adjust equipment parameters flexibly to improve cutting accuracy and efficiency.
Seven Key Points for Maintaining Laser Cutters
The daily maintenance of a laser cutting machine has a direct impact on its life span and processing precision. The key areas of maintenance include cleaning the optical lenses, maintaining the cooling system, and lubricating transmission parts.Regular cleaning of the mirrors can guarantee the quality of the beam, and timely replacement of the cooling fluid can prevent damage from overheating. Standardized alignment of the optical path and backup of parameters can also significantly reduce the risk of operation.Attention to environmental temperature and humidity control and filter replacement cycles are important details that can help keep equipment in top working condition.
Should Small Factories Invest in Laser Equipment?
When it comes to deciding whether to invest in laser equipment, small manufacturers must consider the volume of orders, the appropriateness of the technology, and maintenance costs.Although laser welding and marking can significantly increase efficiency, equipment selection must match actual business needs. The secondhand market also poses hidden risks.The company is advised to lease the equipment for a short term to test its suitability, and focus on whether long-term, stable processing orders can cover the equipment investment, while at the same time doing a good job of preparing a pool of skilled personnel.
Laser Welding in the Auto Industry
Laser welding is revolutionizing the automotive manufacturing industry, from body structures to battery assembly. Its precise and efficient characteristics make it a necessity for modern auto manufacturers.In practical applications, this technology not only increases the strength and airtightness of components, but has also played a key role in the field of electric vehicles.With the integration of auxiliary technologies like laser marking, the automotive production line will achieve an even more intelligent quality control system.
Selecting the Right Welding Method
Material thickness is the key factor in choosing a laser welding method. Thin materials must be welded with a pulsed laser to avoid burn-through. Medium-thickness materials can be welded with a continuous laser, which balances efficiency and quality.In practice, the power, speed, and amount of defocusing must be adjusted according to the characteristics of the material being welded. The parameters must be tested and verified, and attention must be paid to equipment maintenance and real-time observation of the pool of molten metal.
Common Defects and Solutions in Laser Welding
The most common problems in laser welding are the appearance of bubbles, cracks, and uneven welds, all of which can be caused by dirty materials, improper parameter settings, or inadequate maintenance of the welding equipment.By standardizing pre-welding treatment, optimizing power and speed parameters, regularly calibrating the laser beam, and managing the protective gas, the quality of the welds can be effectively improved.Regular attention to the cleanliness of the mirrors, the maintenance of the cooling system, and the control of environmental temperature and humidity can greatly reduce the frequency of equipment breakdowns and extend the life of the laser marker.
Which welding method is best for stainless steel?
In terms of practical performance in stainless steel processing, laser welding has the advantages of precision and efficiency, and is therefore better suited to the precise welding of thin sheets. However, traditional methods such as tungsten inert gas (TIG) welding still have advantages in the processing of thick sheets and in situations where costs are a concern.When choosing the right technology, one must take into account the thickness of the materials, the requirements of the product, and the budget. For export-grade products or for workpieces with a high demand for surface quality, laser welding is still the preferred option.
Cost Comparison of Argon Arc Welding and Laser Welding
In terms of cost structures, laser welding equipment is more expensive, but has lower long-term maintenance and energy costs, and is particularly suitable for precision processing and mass production. TIG welding is more adaptable, and is more suitable for small-scale production.When selecting, one must take into account product accuracy requirements, order size, and labor costs.
What to look out for when maintaining a laser welder
Maintenance of a laser welding machine involves paying particular attention to the cleanliness of the optical components, testing of the core system, and environmental management.The laser head window must be regularly wiped clean, and the power stability monitored. The cooling system filter must be replaced in a timely manner, and the temperature and humidity kept stable.When you use it, get into the habit of warming it up first. If it breaks down, record the code. When you shut it down, cut the power completely.If these details are handled properly, it can effectively extend the life of the equipment and ensure that the welding is precise and stable.
Laser Tattoo Removal: Industry Standards and Regulations
Laser marking in the medical field is directly related to the safety of patients 'lives, and domestic and international standards make strict demands on the durability and traceability of the markings.When selecting equipment, it is important to pay attention to material compatibility certification and daily maintenance requirements. The equipment must meet international standards such as ISO 13485, as well as the specific requirements of GB/T 29490-2023, the latest standard issued in China.Medical devices made of different materials require different laser parameters. Complete documentation and regular calibration are essential to avoiding risk.
A Guide to the Daily Maintenance of a Laser Engraver
The medical industry needs precision control of laser parameters and good material matching, and its maintenance focus is on the cleaning of lenses, monitoring of the cooling system, and maintenance of the guide rails.Each month, the state of the laser should be checked and consumables replaced as needed. Regular maintenance can extend the life of the equipment and ensure the clarity and consistency of the markings.When operating the machine, be sure to wear protective gear, and if any abnormalities occur, immediately stop the machine and check it out. For more specialized questions, contact the manufacturer's technical support.
UV Laser Marking of Absorbable Sutures
Ultraviolet lasers, with their cold processing characteristics, become the preferred solution for marking medical sutures. The micron-level precision and intelligent adjustment functions perfectly accommodate different materials, and the clean control of the entire process and AI quality inspection system ensure that the markings will remain clear over time, while also maximizing the maintenance of material performance, thus providing a reliable technical guarantee for the traceability management of medical devices.
Seven Tips for Improving the Accuracy of Medical Equipment Labels
The precision of laser marking on medical devices directly impacts their safety and traceability, and by using techniques such as choosing the right laser wavelength, optimizing the parameter combination, and maintaining a clean environment, the quality of the marks can be significantly improved.Regular calibration of equipment, updating of software, and use of high-quality consumables are all details that can extend the life of the equipment and ensure stability.By flexibly adjusting processing parameters and pre-treatment methods to accommodate special materials and complex shapes, the company can produce clearer and more reliable markings to meet the high standards of the medical industry.
Standards for Laser Marking of Orthopedic Implants
Medical laser marking technology is at the core of the safety of orthopedic implants, and from the selection of equipment parameters to the details of operation, all must be strictly adhered to.Different materials require different laser wavelengths and energies, and the content of the marking must include traceable information and avoid stress-sensitive areas.The process requires attention to cleanliness and the method of fixation, and the marking must pass a microscope inspection and a corrosion test to ensure its durability. Any lapse in the process could lead to clinical risks and legal disputes.
How to Select Laser Marking Equipment for Medical Devices
Medical device laser marking must take into account the material, the processing precision, and the requirements of the regulations. In choosing equipment, it is necessary to verify the adaptability of the equipment to special materials, to confirm that the precision stability meets the standards of medical certification, and at the same time to consider the service and support capabilities of the supplier.Dynamic focusing technology and intelligent identification software can significantly improve labeling efficiency, and equipment suppliers with complete medical certification can ensure long-term compliance with production standards.
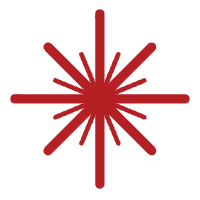
Provides laser marking machine principle characteristics, accessories and software, industry applications, technology optimization, procurement decisions, material technology, technology trends, user scenarios, upgrade solutions, special needs and other related content.